Introducing the ultrasonic wire welding machine: a revolutionary tool that utilizes high-frequency vibrations to precisely and securely weld wires together. This advanced technology is indispensable in industries such as automotive and electronics, where reliable electrical connections are critical. Unlike traditional methods like soldering or adhesive bonding, ultrasonic welding ensures cleaner, faster, and more consistent results, optimizing production efficiency and reducing costs. These machines integrate seamlessly into automated assembly lines, enhancing workflow and productivity. Discover how our state-of-the-art welding solutions elevate manufacturing standards, providing robust wire harness assemblies that meet stringent quality and performance requirements.
Products
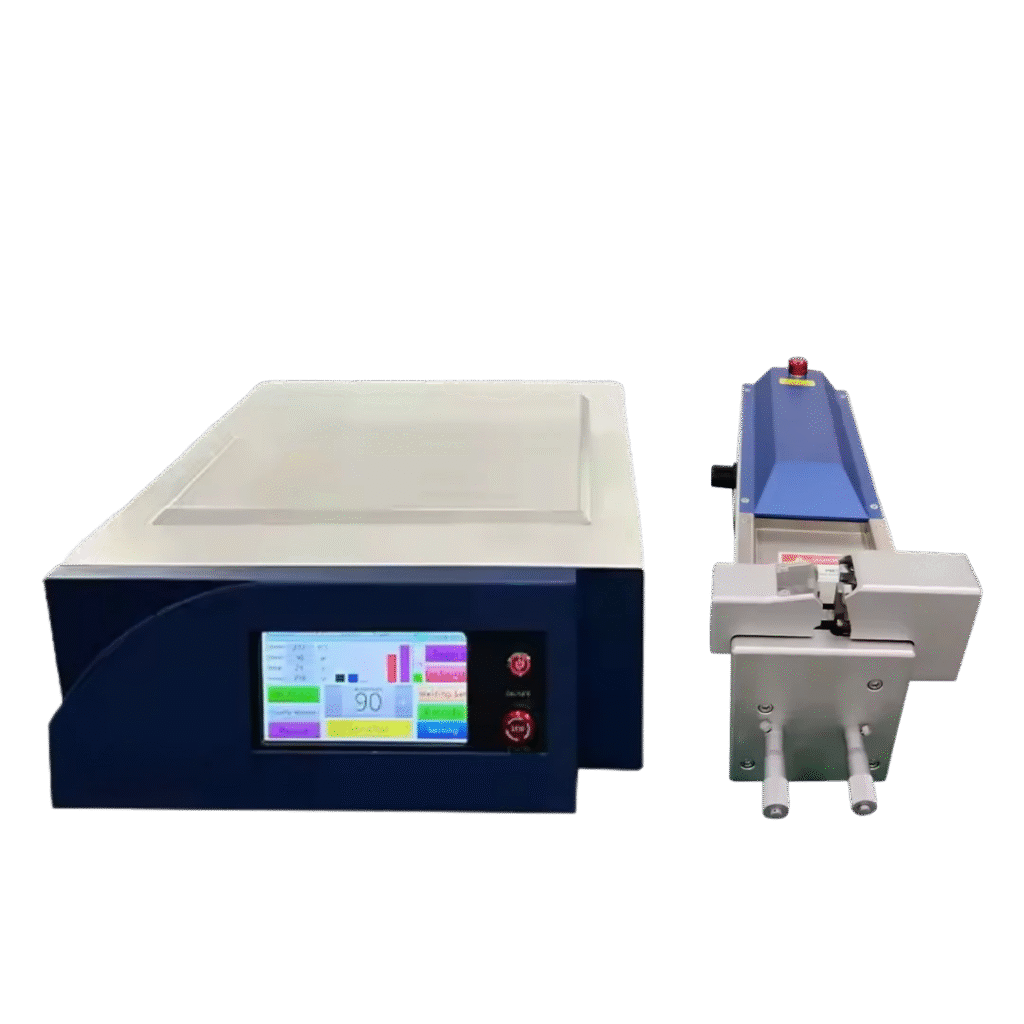
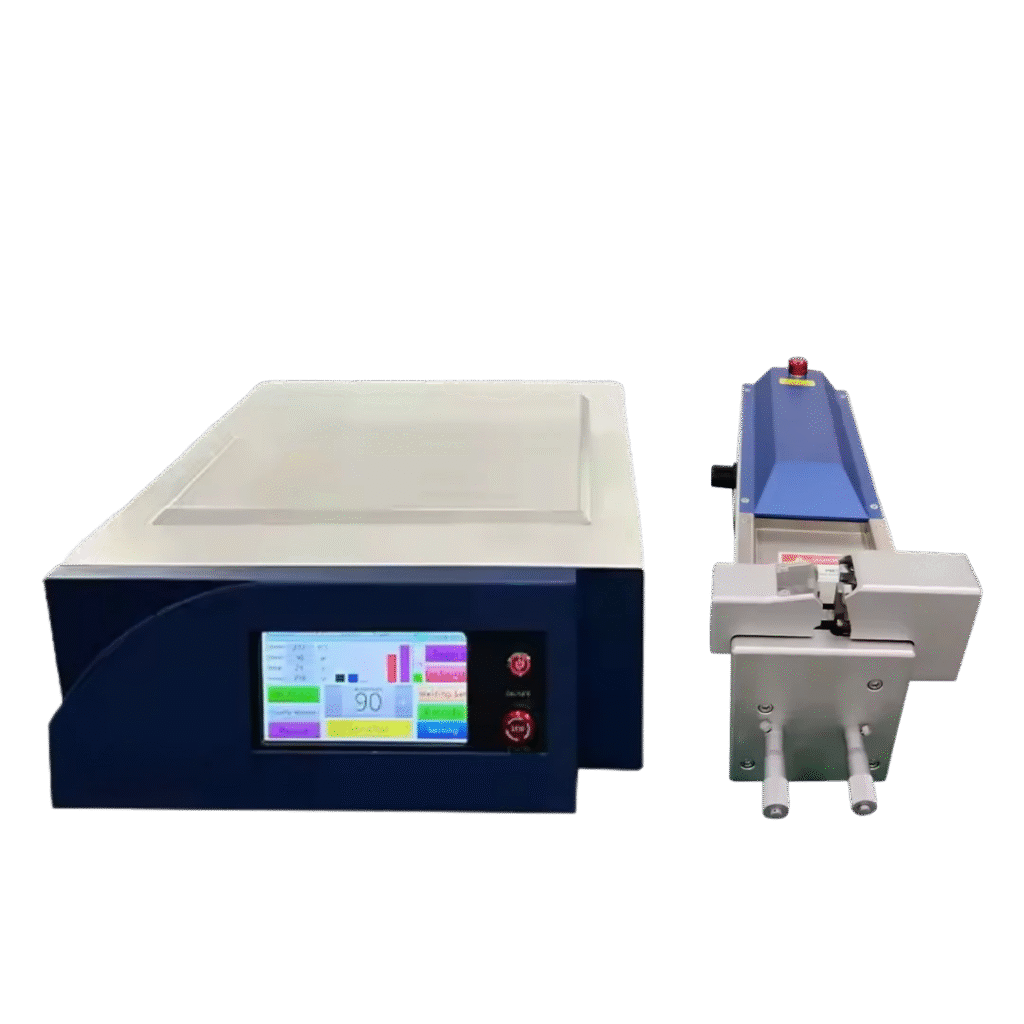
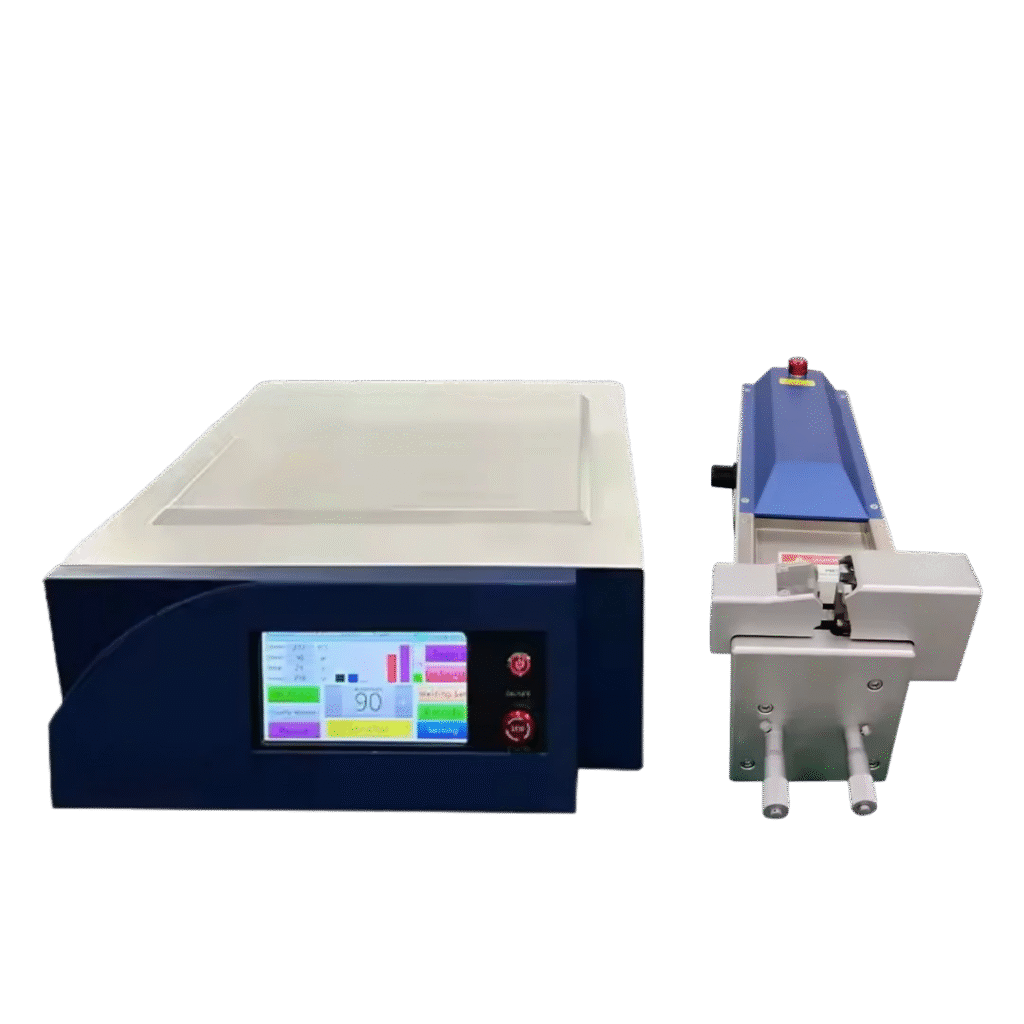
Uses
Ultrasonic wire harness welding machines are used to join wires and terminals without the need for soldering or adhesives. This process is commonly employed in industries where reliable and robust electrical connections are critical.
Applications
- Automotive Industry: Ultrasonic wire harness welding is used extensively in the automotive sector to create strong, reliable connections for wiring in vehicles.
- Consumer Electronics: Ensuring durable and efficient connections in small electronic devices.
- Aerospace: Provides lightweight and high-strength connections for aerospace wiring systems.
- Home Appliances: Used in the manufacturing of home appliances for reliable electrical connections.
- Medical Devices: Ensures precision and reliability in medical device wiring.
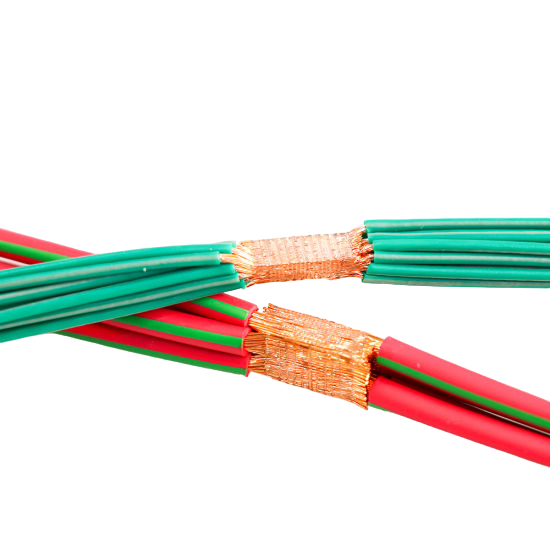
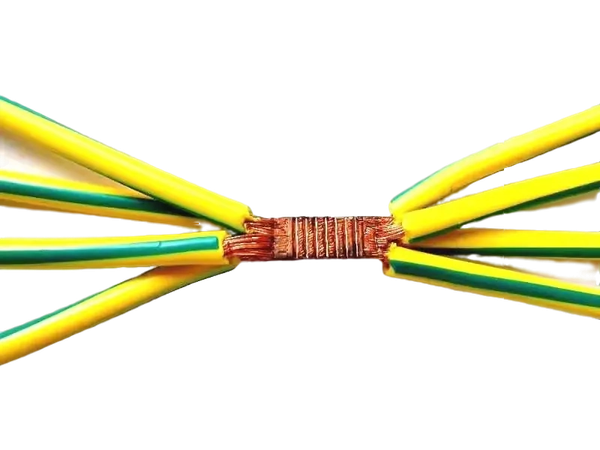
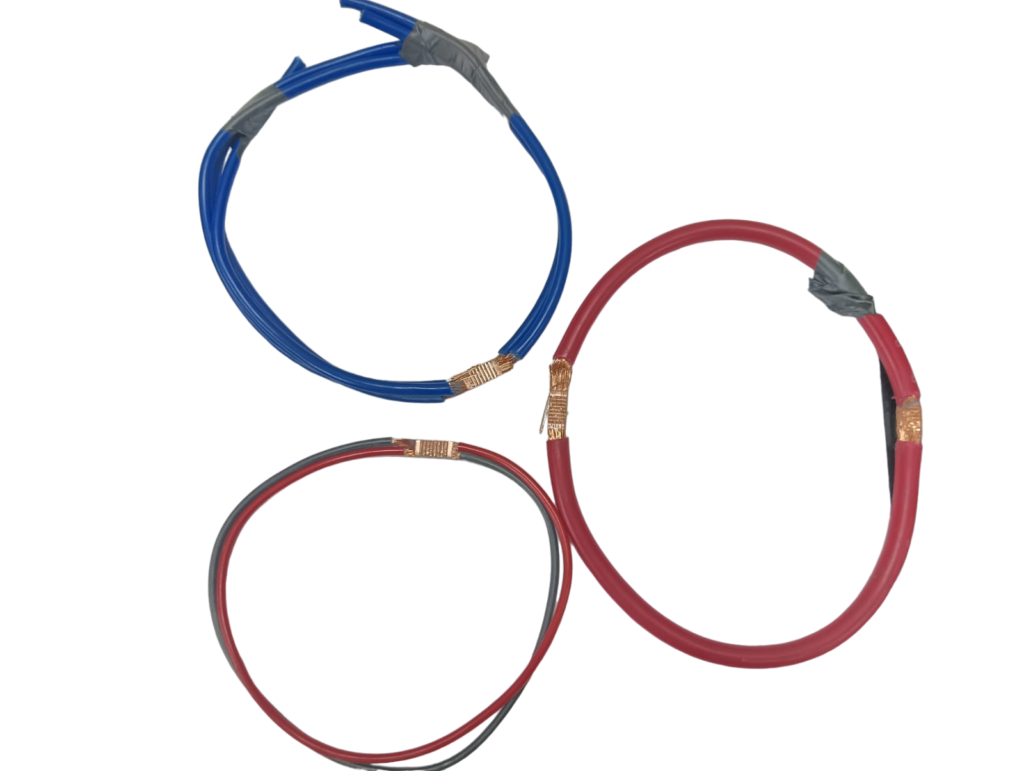
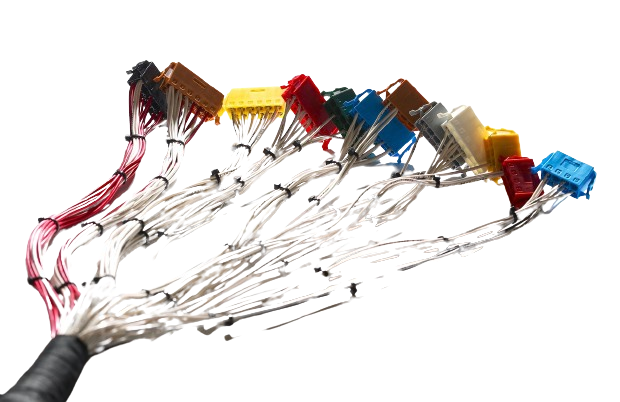
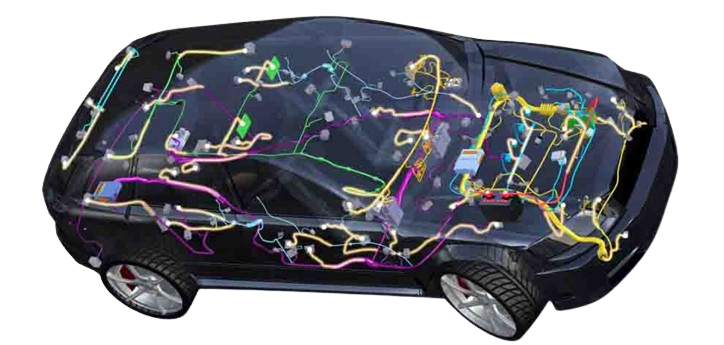
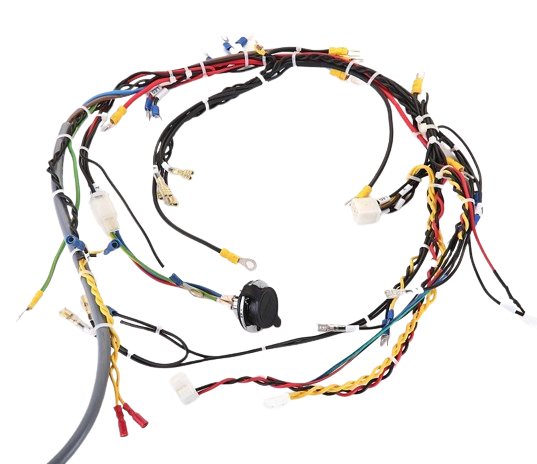
Features
- Efficiency: Quick welding process that reduces production time.
- Consistency: Provides consistent welds with high precision.
- Quality: Produces high-quality connections that are robust and durable.
- Environmentally Friendly: No need for adhesives or solder, which reduces waste and potential contaminants.
- Energy-Efficient: Uses less energy compared to traditional welding methods.
- Non-Destructive: Does not damage the wires or surrounding insulation.
- Automation Compatible: Can be integrated into automated production lines for high-volume manufacturing.
Why Choose Dhruv’s Ultrasonics?
- Reliability: Dhruv’s Ultrasonics are known for their reliability and durability in industrial applications.
- Advanced Technology: Incorporates the latest ultrasonic welding technologies to ensure efficient and high-quality welding.
- Customization: Offers customized solutions tailored to specific industry needs.
- Support and Service: Provides excellent customer support and after-sales service.
- Cost-Effective: Competitive pricing with a focus on long-term value.
Why Use Ultrasonic for Wire Harness?
- Speed: Ultrasonic welding is faster than traditional methods.
- Strength: Creates strong, reliable bonds that can withstand harsh conditions.
- Safety: Eliminates the need for open flames or hazardous chemicals.
- Consistency: Ensures uniform connections with minimal variation.
- Cleanliness: No residue or waste products, making it a clean process.
Where is Ultrasonic Wire Harness Welding Used?
- Automotive manufacturing plants
- Electronics manufacturing facilities
- Aerospace production lines
- Medical device assembly
- Home appliance factories
Why Choose Lingke Brand Machine?
- Quality: Lingke machines are known for their high-quality construction and components.
- Innovation: Continually innovates to improve efficiency and performance.
- User-Friendly: Designed with user-friendly interfaces and easy operation.
- Global Presence: Established global presence with a network of distributors and service centers.
- Reputation: Strong reputation in the industry for reliability and customer satisfaction.