In today’s fast-paced manufacturing world, industries are constantly evolving to meet the demand for faster, cleaner, and more reliable joining technologies—especially when working with conductive metals like copper, aluminum, and nickel. Traditional welding techniques, though widely used, often involve high heat, toxic fumes, melting, and post-processing steps that compromise efficiency and material integrity. Ultrasonic Metal Welding (UMW) emerges as the game-changing solution that addresses these challenges head-on.
At Dhruv’s Ultrasonics, we design and deliver high-performance ultrasonic metal welding machines that offer unmatched reliability, precision, and adaptability across sectors such as EV battery production, solar panel assembly, wire harness manufacturing, and power electronics.
This blog offers an in-depth look into the principles, advantages, applications, machine models, and real-world benefits of ultrasonic metal welding for modern industries.
Hot Selling Ultrasonic Metal Welding Machines
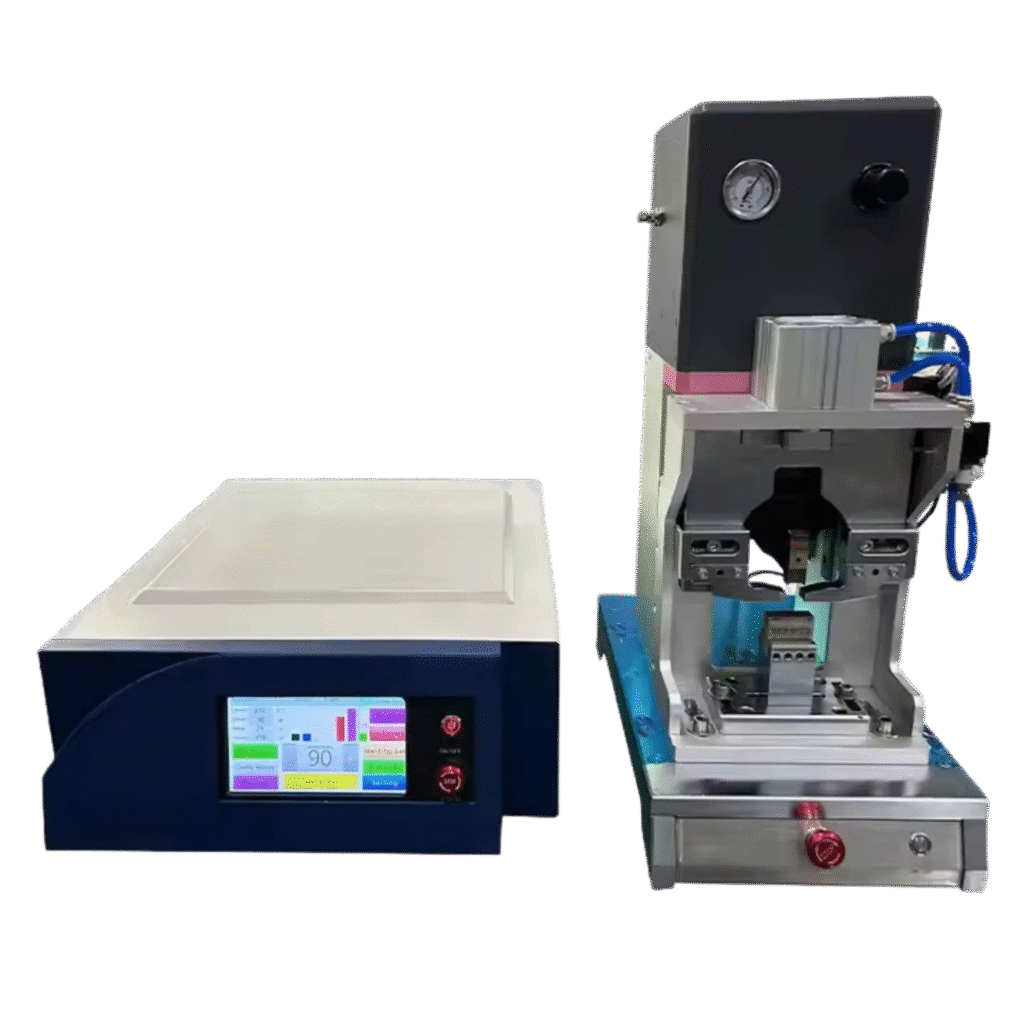
Parameter | Specification |
---|---|
Frequency | 20 Khz |
Power | 3000 Watt |
Input Voltage | AC 220 Volt |
Weld Area Capacity | Up to 20 mm² |
Amplitude Adjustment | 10% to 100% |
Welding Modes | Time, Energy |
Control Interface | Digital Touchscreen |
Cooling System | Air |
Horn Material | Titanium |
What is Ultrasonic Metal Welding?
Ultrasonic Metal Welding is a solid-state welding process that uses high-frequency ultrasonic vibrations (typically around 20 kHz) combined with moderate pressure to bond two or more pieces of metal. The metals are not melted; instead, they are bonded through localized friction, plastic deformation, and diffusion at the contact surfaces.
This process is clean, energy-efficient, and ideal for joining thin, conductive, and dissimilar metals without the need for solder, adhesives, or flux.
How It Works:
- The machine generates high-frequency ultrasonic energy using a transducer and booster.
- This energy is transferred to a welding horn (sonotrode) that contacts the metal surface.
- The vibration and pressure generate localized heating through friction, causing the atoms at the contact point to rearrange and form a metallurgical bond.
- Within seconds, a strong, clean weld is formed without altering the bulk properties of the base material.
Why Use Ultrasonic Metal Welding?
Traditional welding methods such as arc welding, laser welding, or soldering rely heavily on melting the base materials. This often leads to:
- Thermal damage
- Material warping
- Oxidation
- Weakened electrical conductivity
Ultrasonic welding eliminates all of these issues. Here’s why it stands out:
- No Heat Damage: It’s a cold weld process. There’s no melting, so thermal degradation is avoided.
- High Conductivity: Produces joints with near-zero resistance—critical for electrical and battery systems.
- Eco-Friendly: No smoke, fumes, or flux required—making it safe for operators and the environment.
- Fast & Repeatable: Welds complete in under a second, perfect for high-volume production lines.
- Strong & Durable Bonds: Reliable even under mechanical stress, vibrations, or extreme environments.
Key Components of an Ultrasonic Metal Welding Machine
At Dhruv’s Ultrasonics, each machine is engineered with industrial-grade quality and digitally intelligent systems.
Main Components Include:
- Ultrasonic Generator: Converts electrical energy into high-frequency signals.
- Transducer: Converts electrical energy into mechanical vibrations.
- Booster: Amplifies the vibrations to suitable amplitudes.
- Horn (Sonotrode): Applies the vibration and pressure directly onto the workpiece.
- Fixture/Clamp: Holds the metal parts in place during welding.
- Control System: Touchscreen or PLC interface for setting welding parameters.
Use Cases Across Industries
Ultrasonic metal welding is used in virtually every industry where high-conductivity, strong bonding, and miniaturization are critical.
Popular Application Areas:
Industry | Common Applications |
---|---|
Electric Vehicles (EV) | Battery tab welding, busbar bonding, terminal fusing |
Solar Energy | Foil joining, interconnect welding, junction bonding |
Wire Harness Manufacturing | Wire splicing, cable-to-terminal, aluminum wire joining |
Electronics & PCBs | Micro-welding for connectors, sensors, and modules |
Medical Devices | Connector assembly, battery pack welding |
Aerospace & Defense | Shielded cable joining, sensor bonding |
Power Distribution | High-voltage busbar-to-cable connections |
Consumer Goods | Battery cell tabbing, smart device terminal bonding |
What Can You Weld with Ultrasonic Metal Welding?
One of the biggest advantages is its versatility with non-ferrous and dissimilar metals.
Compatible Materials:
- Copper (solid or stranded)
- Aluminum
- Nickel
- Silver
- Lithium foils
- Tin-coated conductors
- Gold-plated connectors
- Bi-metallic joints (Cu-Al, Ni-Cu, etc.)
Note: Ultrasonic metal welding is not suitable for ferrous metals like steel or stainless steel, as their molecular structure doesn’t deform easily under ultrasonic vibration.
Machine Models Offered by Dhruv’s Ultrasonics
We offer a range of high-performance machines designed for different applications and scale of operation.
Our Ultrasonic Metal Welding Models Include:
Model | Frequency | Power Output | Suitable For |
---|---|---|---|
DU-20K/3000W | 20 kHz | 3000 W | Wire harness, foil joining |
DU-20K/5000W | 20 kHz | 5000 W | Busbars, terminals, multiple conductor |
DU-20K/7000W | 20 kHz | 7000 W | Heavy-duty copper cables |
DU-20K/10000W | 20 kHz | 10000 W | Thick foil stacks, automotive busbars |
Each system is automation-ready, featuring:
- Auto-frequency tracking
- Digital touch control
- Safety interlocks
- Custom horns and fixtures
- Real-time weld monitoring